The Brief Life of the Twin Cat
In the world of aerial application, innovation has always been key to tackling unique challenges, whether it’s crop spraying, pest control, or fire fighting. The aircraft used for these demanding tasks have evolved distinctly from other aviation categories, often requiring creative modifications to enhance safety and efficiency.
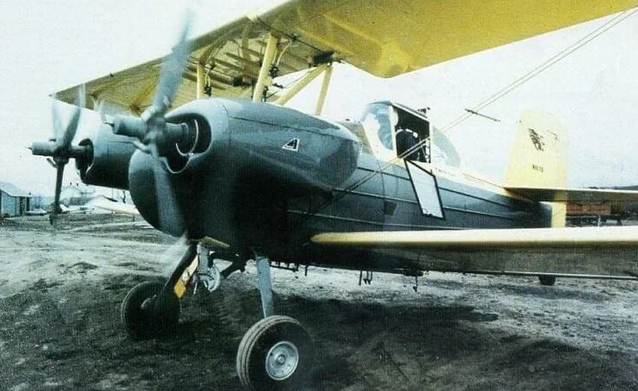
Photo Source: https://www.reddit.com/
One such innovation was the “Twin Cat,” a unique variant of the 1950s-era Grumman Super Ag Cat biplane, which emerged in the late 1970s and early 1980s. This aircraft replaced the original Ag Cat’s single 600 hp Pratt & Whitney R-1340 radial engine with two 310 hp Lycoming TIO-540 flat-6 engines.
Unlike a typical factory-built aircraft, the Twin Cat was a modification offered via a supplemental type certificate (STC). The Twin Cat Corporation aimed to provide Ag Cat operators with more serviceable engines, extended overhaul intervals, and the added safety of multiengine redundancy. The company even offered on-site modifications for customers.
The leadership behind the Twin Cat had notable experience. The president had previously overseen a turboprop conversion of the Grumman Albatross, and he was supported by the former chief test pilot at Rockwell International’s general aviation division. Test flights were led by Herman “Fish” Salmon, a retired chief engineering test pilot from Lockheed, who had a storied career including spin testing the P-38 Lightning and flying the first flights of several notable aircraft like the L-188 Electra and YF-104A Starfighter.
A key design priority for the Twin Cat was minimizing asymmetric thrust in case of an engine failure. To achieve this, the engines were mounted on either side of the nose with only about 3.5 feet between the propeller tips. Additionally, the engines were canted slightly outward, further reducing asymmetric thrust during single-engine operations.
The Twin Cat boasted several advantages beyond the engines’ 2,000-hour time between overhauls (TBO) and improved parts availability. Although the engines were rated at 310 hp each, they were effectively derated “with a pencil” to provide up to 350 hp when necessary. Remarkably, the Twin Cat’s total fuel consumption matched that of the single-engine radial Ag Cat. The new engine layout also improved forward visibility, prop clearance, and spray dispersion.
Flight testing was crucial to validate the Twin Cat’s performance. Despite having the same empty weight as the Ag Cat at 3,500 pounds, the Twin Cat had a maximum takeoff weight of 6,500 pounds, 2,000 pounds higher. The aircraft featured a load jettison function, allowing the pilot to dump 2,000 pounds of payload if needed.
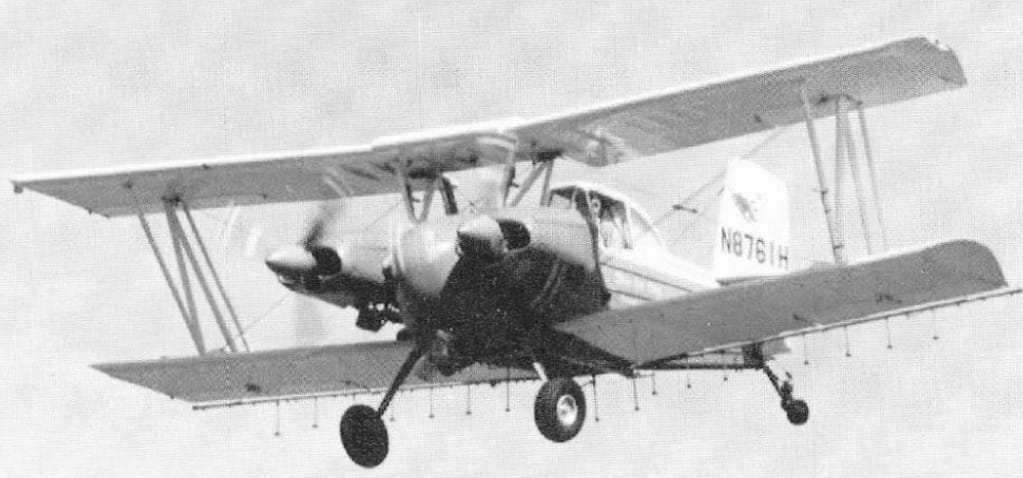
The new engine configuration proved effective. The Twin Cat’s takeoff distances were about 20 percent shorter than those of the Ag Cat. Asymmetric thrust was so well managed that the aircraft could take off with one engine shut down and still climb at 400 feet per minute at sea level. This capability was marketed as a way to ferry the aircraft to a maintenance location with one inoperative engine.
In flight, the Twin Cat could cruise at a maximum speed of 130 knots. The slightly downward-canted engines contributed to a low stall speed, claimed to be 49 knots for power-off stalls and 43 knots for power-on stalls. A brochure even asserted that the Twin Cat had “no VMC,” allowing flight down to stall speed without controllability issues.
However, some reports suggested the Twin Cat needed further refinement. It reportedly lacked rudder trim, and with one engine shut down, a pilot had to reduce power on the functional engine to maintain control due to running out of rudder authority. It remains unclear if the company intended to introduce rudder trim in future versions.
Ultimately, only three Twin Cats were rumored to have been completed and flown. One reportedly crashed, while the others likely reverted to their original single-engine configuration after the company decided to discontinue the project. Thus, the Twin Cat remains a brief, intriguing chapter in the history of aerial application aircraft.